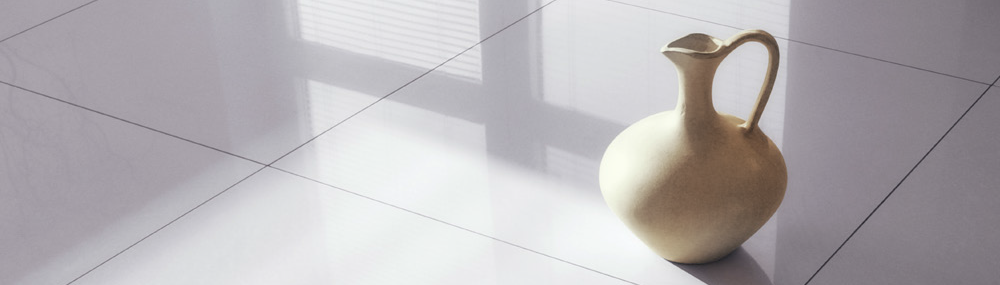
Ceramic Rollers
Ceramic tile production exceeds 10 billion m² worldwide each year, making it one of the most popular choices for household, recreational, business and industrial applications. Tile sizes vary, but certainly there is a trend towards larger pieces, which are difficult to make with flat surfaces.
Many of the rollers used today are alumina-containing. Alumina rollers outperform other materials because of its mechanical strength and creep resistance under high temperature and load conditions, which is particularly important in the firing of large tiles. Alumina rollers also have a longer application service life than other materials, making it the clear choice for high performance roller products.
Almatis offers specific tabular and calcined alumina products for ceramic roller production. Our particle size distributions are advantageous as compared to white fused alternatives due to higher particle packing. Ground calcined products can be added to increase alumina content and strength properties.
Unground Calcined Aluminas
Primary Crystal Size = 1.1µm
Specific Surface Area = 1.2 m²/g
Na2O Content = 0.06%
Continuous Ground Calcined Aluminas
Ground Median Size = 3.5µm
Ground Surface Area = 0.90 m²/g
Na2O Content = 0.12%
Ground Median Size = 3.4µm
Ground Surface Area = 1.0 m²/g
Na2O Content = 0.12%
Batch Ground Reactive Aluminas
Ground Median Size = 0.4µm
Ground Surface Area = 8.8 m²/g
Na2O Content = 0.07%
Ground Median Size = 0.4µm
Ground Surface Area = 7.5 m²/g
Na2O Content = 0.08%
Ground Median Size = 0.6µm
Ground Surface Area = 8.2 m²/g
Na2O Content = 0.07%